What is Poka-Yoke?
Last Updated April 22, 2022
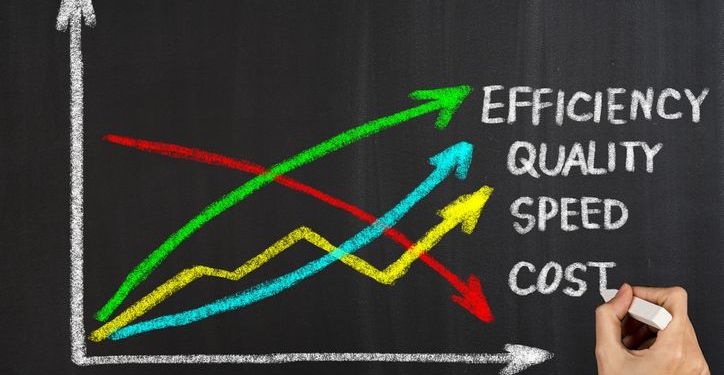
The Value of Poka-Yoke: A Proven Way to Make Processes Error-Proof
Many of the defects, variation and inefficiencies in our processes are caused by human error. Poka-yoke (pronounced “poh ka yoke”) is a simple but powerful and effective means of preventing or detecting mistakes caused by people. Poka-yoke was developed as a key component of the Toyota Production System (TPS), but the tool can prove useful in any industry.
Also known as error-proofing, poka-yoke is a method for taking steps to mistake proof a process. It is a foundational tool of both Lean, which targets waste, and Six Sigma, which focuses on defects, with a goal of eliminating every mistake by creating systems that either immediately prevent or detect them. Poke-yoke reduces the waste caused by defects, which can help improve efficiency and save costs in rework or additional processing.
Poka-yoke is an ongoing process. One of the key factors that too often is ignored in continuous process improvement is the “continuous” part. Poka-yoke provides for that, creating solutions for mistakes that take care of the issue going forward, not for just one instance.
How important is poka-yoke? It’s still a key part of the Toyota Production System, as a feature of the Jidoka system, one of the two pillars of the TPS. Jidoka identifies the causes of problems and allows for the stopping of a process by man or machine rather than producing something defective.
Defect Detection
According to the TPS, poka-yoke is the use of any type of automated device or other method that either stops a process if an error is about to be made or makes it known immediately that an error has happened.
Examples of poka-yoke include:
- When filling out forms online, software programs will not let users hit the submit button until they have filled every required field, keeping the forms from having mistaken and incomplete information
- Electronic healthcare records can perform various types of poka-yoke operations, such as giving doctors a red flag if they prescribe medication that might interact negatively with medication the patient is already taking
- Chiming or alarm sounds at an ATM machine indicating the customer should retrieve their debit card has greatly reduced a once-frequent problem – people driving off and forgetting their card in the machine
- The “spell check” function on most programs created for writing, including Word, Google docs and PowerPoint has helped limit the number of spelling errors
The Origins of Poka-Yoke
The ideas that became poka-yoke were introduced by Shigeo Shingo, an industrial engineer who went on to develop several of the tools and techniques still vital to Lean and Six Sigma today.
In 1961, Shingo visited a plant where a very simple assembly procedure was resulting in defective parts being sent to the parent company. The cause of the problem was that employees were forgetting to put springs into an on/off switch. The parent company tried to resolve the issue by sending an inspector, but it was time-consuming and expensive.
Shingo realized two truths: sometimes we forget things, and sometimes we also forget that we have forgotten something. Having reached the root cause of the problem, Shingo started to design ways to error-proof operations and help people remember their job requirements. This included creating checklists for each day on the job.
As processes changed, so did the lists. Initially, Shingo called these error-proofing methods baka-yoke, which essentially means “idiot proof.” But this put the focus on the person, not the operation. It also caused one employee to burst into tears and declare “I am not an idiot!”, according to an article in the Harvard Business Review (HBR) titled, “Poka-Yoke is Not a Joke.”
Thus, Shingo changed the name from the harsher “idiot-proof” to the milder “mistake-proof,” because his goal for poka-yoke was for it to help eliminate mistakes as simply and cost-effectively as possible.
Applying Poka-Yoke
The HBR article notes that poka-yoke’s no frills, practical approach to preventing mistakes or immediately detecting them may be one of the most important aspects of Lean methodology.
In business, mistakes cost money and hurt the bottom line. In other professions, the stakes are higher. For example, a healthcare professional making a small mistake (wrong medication, missed suture during surgery) can cause serious health emergencies.
Even if the mistakes don’t seem immediately consequential, poka-yoke is important. As pointed out in the HBR article, nothing undermines professionalism quite like an easily avoidable mistake – think Excel miscalculation, a PowerPoint misspelling or a misplaced email. Such small errors could have the potential to hurt a business negotiation, damage customer satisfaction or cost a company business.
Learning Poka-Yoke
The focus of Lean and Six Sigma is to identify and eliminate waste and defects. Poka-yoke plays a big role in that area. For professionals who desire to take on a leadership role in improving business operations, earning a Six Sigma belt and certification is a smart first step.
Click here to learn about Villanova’s Certificate in Lean Six Sigma program and how you can qualify for Villanova’s 100% online Lean Sensei, Six Sigma Green Belt and Lean Six Sigma Black Belt certification exams.