Understanding Lean Six Sigma Metrics
Last Updated February 6, 2018
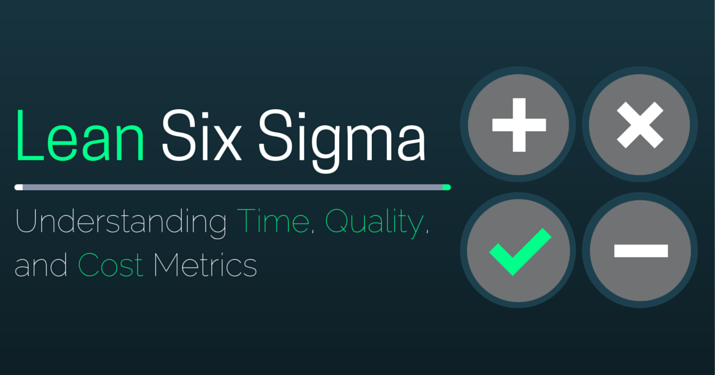
What is not measured is not managed. This is an important adage to keep in mind when designing Lean Six Sigma programs, which are intended to meet objectives for creating continuous improvement in processes across an organization.
Well-organized metrics are important because they help to better identify areas where a process can be improved. Detailed metrics can also help measure the effectiveness of Lean Six Sigma initiatives. Done correctly, they can aid management in identifying defects in the business, such as causes of waste, variability or customer dissatisfaction. If metrics are carefully monitored, they may help diagnose the root of the problem, as well as list several key areas for improvement.
Here is an overview of three main Lean Six Sigma metrics, and how businesses can apply them to future initiatives:
Time
This metric helps gauge the amount of time it takes to produce a product or service while also factoring in the amount of processing time versus process idle time. There are several areas the time metric measures. It can measure the lead-time for a process, which is how much time it takes to develop the product/service beginning to end, from the customer’s point of view.
It also measures process completion times, from best to worst, and it assigns a value to each process, which helps determine what processes are continually living up to or falling short of business expectations. Another measure that the time metric quantifies is the activity ratio, which is determined by dividing the processing time by the lead-time. This helps determine the actual time it takes to make a product or service and ship it out to the customer.
Cost
It is important to define the cost to operate a process, as well as determine whether it is costing the company too much money to run. Cost measures labor, cost-per-product and savings, and helps measure the amount of labor, material and overhead needed to produce a quality product or service.
Quality
The quality metric helps quantify issues relating to process errors that may require revisions, and can assist businesses in improving the customer experience. It also can help measure a ratio of work completed that’s accurate and on-par with industry standards. Monitoring the quality metric is important for understanding how often a product or service advances through the entire process, and can help limit the number of errors associated with the process.
The type of metric used can depend on factors of the project, but a good rule of thumb is to use a metric that fits the project goals. It’s also recommended to include one metric for the initiative that may be meaningful to the customer, and another metric that is relevant to the business’ leaders and strategic goals.