Taking a Gemba Walk
Last Updated March 17, 2020
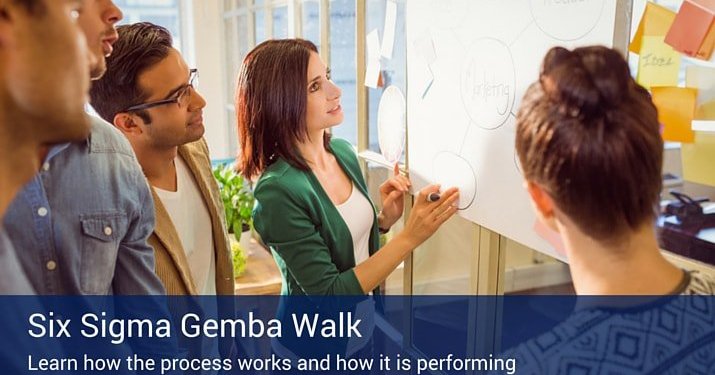
Imagine your Six Sigma project team being in danger of losing touch with the process that it’s trying to improve. How can this be when your team focuses so intensely on every aspect of the process they are improving? They gather extensive data on process performance, exhaustively analyze every step of the process and work tirelessly to find new ways to improve it.
Wouldn’t this close connection ensure that your team has a solid understanding of how the process works and how to improve it?
The risk is not that your team will fail to understand the process, but that the team will begin to see the process as a theoretical abstraction that exists only on a white board, and produces only numbers on a spreadsheet. Project teams begin to lose their way when they forget that a process consists of real people doing actual work that affects real-life customers.
This happens when team members begin to become removed from the process. When a team is physically distant from the process, it will develop only a vague understanding of how the process truly works. That vague understanding produces inadequate improvements.
Keep It Real with a Gemba Walk
The best way to prevent the process that your team is improving from becoming a vague theory is to step out of the conference room and visit the production line, factory floor or service center where the process actually lives.
Japanese quality professionals call this a Gemba: meaning “real thing” or “the real place.” The Gemba Walk originated in Japan and is now being applied in companies all over the world.
Taking a Gemba walk requires a manager to schedule 10 to 15 minutes on a regular basis for the Six Sigma team to visit the shop floor. The team takes time to speak to line managers and front-line workers to learn how the process works and how it is performing.
Your project team can obtain the benefits of the Gemba Walk by keeping a few simple principles in mind.
- Do it right – The Gemba Walk is a chance for your team to observe the process and learn how it is working. It is not an opportunity to talk about problems and propose solutions, to criticize the process or to record complaints from workers.
- Look closer – The purpose of the Gemba Walk is to give project teams a chance to observe the process in action. Quiet and attentive observation helps team members understand the process better. It also plants seeds in team members’ minds that, when nourished with reflection and discussion, often bloom into new and innovative ideas.
- Not MBWA – Years ago leaders were encouraged to practice “management by walking around” (MBWA). This involved managers randomly wandering the factory floor hoping to stumble upon obvious problems they might be able to solve. The Gemba Walk is different in that it requires a purpose. Team members must know why they are observing and what they are trying to learn.
Don’t let the team forget that the project you’re improving is not just an abstraction on paper. It is a real processes manned by real people. Ten minutes of live observation can teach your team more about the process than ten hours of theoretical conversation.
How Does Gemba Actually Work?
Here are five ways in which a Gemba Walk can help your team understand a process better.
- Focuses Attention – Team members face a daunting number of tasks that compete for their time and attention and pull them away from their Six Sigma duties. Activities such as meetings, phone calls, emails, planning and, of course, their daily work responsibilities, sidetrack team members from process improvement.Participating in a Gemba Walk helps put key people in front of the functioning process, allowing them to see it in action and focus directly on the process.
- Creates a Common Vision – Team members may say that they understand the process, and all may claim to see it the same way. Every team member may even use the same words to describe the process you’re working on. Don’t fall into this misperception. Each team member likely sees and understands the process slightly differently. Some differences are subtle, some are dramatic.Gathering all members of the project team together in the same place at the same time to observe the same process in action is one of the most powerful tools available for creating a common understanding of the process.
- Includes Real-Life People – Front-line workers have their minds on the process every single day, and they are critical in determining product quality. These workers are experts in how the process works. A Gemba Walk gives project teams a chance to talk to these workers face to face and learn where the process works well and where it could benefit from change.
- Gives the Big Picture – Project teams tend to rely heavily on graphical data displays such as Pareto Charts, Histograms and Run Charts to measure how well the process is performing. While these tools are helpful, they have one serious deficiency – they may not be measuring the right thing.If your team never leaves the conference room, and its only interaction with the process is a paper printout displaying the past performance of one aspect of production, your solutions will likely be incomplete.When your team members understand the entire process, because they have seen it in action, they are far more likely to evaluate all aspects of the process, and not just a few of the most obvious ones.
- Primes the Subconscious Mind – The interworking of the mind and senses are beyond the scope of Six Sigma methodology, but they play an important role in problem solving. Project teams can gain a powerful understanding of the process by taking a Gemba Walk, but it is only the tip of the iceberg.Every second the human senses send the brain over 11 million bits of information. The conscious mind is only aware of 50 bits of this information. Using the same 220,000 to 1 ratio it could be said that for every insight, observation and idea that a team member gains from a Gemba Walk, there are 220,000 others locked away in the subconscious mind. Planting this raw material in your team members’ minds helps them produce more creative insights and more effective solutions.
Don’t lose touch with the process that your team is trying to improve. Take a Gemba walk and see that the process consists of real people doing real work for real customers. When the process is real to your team, you can generate much more creative solutions and implement better improvements.