Six Practical Lean Six Sigma Tools to Eliminate Waste, Streamline Flow and Increase Efficiency
Last Updated February 11, 2021
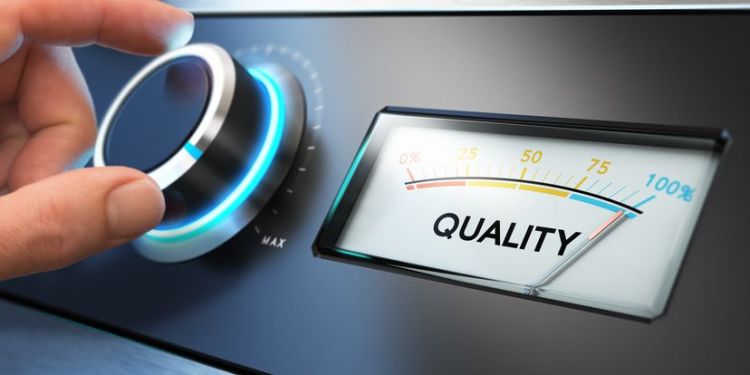
Lean Six Sigma offers a proven methodology with tools and techniques that empower people to take better control of how an organization operates.
The methodology requires leadership buy-in, correct implementation and education to teach practitioners how to master its principles. The goal is a more efficient and effective operation.
This article will explain six tools from the Lean Six Sigma methodology that professionals can use to help improve processes and project outcomes. The goal of each tool is practical in nature and offers systematic approaches to solving seemingly intractable problems.
The Five Whys
The Five Whys helps identify the root cause of a problem and may be one of the most practical tools in Lean Six Sigma’s arsenal.
The Five Whys requires asking a series of “why” questions (typically five or less) that can help project teams understand the heart of the problem and how to take action to correct it. The process starts with a statement of a problem.
For example:
- We are always late getting our shipment to client X.
- Department A does not receive the information it needs from Department B.
Then, a series of “why” questions are asked to dig deeper into the issue until a root cause is found. Using the Five Whys can help organizations identify the root cause of the issue rather than dealing with the symptoms of the bigger problem.
Keep in mind that the Five Whys could lead to a variety of conclusions for different levels of an organization. For example, using the tool for the question “why did the Titanic sink?” could lead to an operations issue (lookouts didn’t see the iceberg soon enough), an executive issue (they were going too fast) or a design issue (the hull wasn’t built to keep water from flowing from one compartment to another). All, however, are valid causes.
Poka-Yoke
Poka-yoke is a method for taking steps to mistake-proof a human process. It operates under the assumption that, frequently, small changes can fix a larger problem. The goal is to eventually have zero defects. With poka-yoke, people from any stage of an operation can develop an idea for the change. The emphasis with poka-yoke is on executing plans and analyzing the results.
One example is the software program that controls an online form and requires filling in every field to move to the next page so the user does not have to waste time redoing an incomplete application.
Control Charts
A control chart helps analyze the differences in a process before and after changes are made. Its most common use is to create a chart that indicates the stability of a process. Data is gathered on an operation’s key characteristics and outcomes. A chart is then made showing the range of variation in these areas. The less variation, the better.
A control chart is a practical, effective way to visualize the consistency and stability of a process. It allows practitioners to see a process over time and provides more predictability than raw data. Using a hospital setting as an example, a control chart might show the results of the process of putting new patients into the system at a hospital emergency room. It could also show the usual time it takes to enter the information into the system and how long it takes for the right clinical personnel to arrive. In this case, time is the important variable. Hospitals want a consistent track record of how long it takes to get a patient from intake to the care they need.
Value Stream Mapping
A value stream map is a tool typically used in Lean that can help organizations identify and eliminate waste along the entire cycle of a process. Value stream mapping takes a higher-level view of an operation and requires mapping out every step of the process from beginning to end, supplier to customer. Each task along the way is considered through the lens of the value it brings to the final product. A value stream map can help identify areas where further steps need to be taken and can visualize the eight forms of waste in Lean – defects, over-production, waiting, non-utilized talent, transportation, inventory, motion and extra processing.
The Lean Six Sigma course, one of the two required courses in Villanova’s Certificate in Lean Six Sigma program, teaches that the first rule of value stream mapping is to start with a simple, basic map to focus on the major process steps and to help avoid confusion. Next, maps should be created by team members and compared, allowing each person to see what was created. The final rule of value stream mapping is to ensure the team leader trains everyone on how to create a proper value stream map, one that does not contain team member bias.
Cause and Effect Diagram
Sometimes known as a Fishbone Diagram (because of its shape), a Cause and Effect Diagram is a graphical tool used to display causes associated with a specific event. Each cause is then organized into categories to help determine potential causes for problems. Using it can involve application of the Five Whys and other methods used to find root causes of operational problems.
Take, for example, the hypothetical issue of why the correct stakeholders are not being invited to a creative meeting. Meetings are often rescheduled because a needed person is not in the room.
Why does this happen? Some potential causes could be:
- The email distribution list for the meeting is old
- The person in charge of the meeting is not in charge of the email distribution list
- The person in question has a conflicting meeting
- The person in question works remotely the day of the meeting
Of course, the meeting participants could gather in a room and come up with reasons for the problem without a diagram. However, the Cause and Effect Diagram is all about scope, a focused form of brainstorming where potential causes are identified by category. There may be several reasons why stakeholders are not in a meeting. Taking the time to document those reasons can help increase the chances of coming up with a solution to the problem.
Takt Time
Takt time is the rhythm of production and the amount of time that each product or service must be delivered within to meet customer’s demand. First, the rate of consumer demand (on average) must be determined. Then, how much time is needed to deliver the product or service is measured against that demand rate.
This process serves two main purposes. First, it ensures that the rate by which a product or service is being done meets consumer demand. Second, it ensures that too much of a product is not made, cutting down on the time a product spends in inventory.
The first documented use of Takt time was in German aircraft manufacturing in the 1930s. Toyota later applied Takt time to determine the best cycle time for making cars. Today, a restaurant could use it to determine the production cycle needed to make enough food to meet expected demand, but not so much that food goes to waste.
These are some of the tools and techniques employed in Lean Six Sigma to help make operations more effective and efficient. Gaining knowledge and competency in these areas can help you prepare for industry certification, identify and eliminate defects and waste in your organization and sustain processes to help increase your productivity.