Production Manager Job Description
Last Updated October 24, 2019
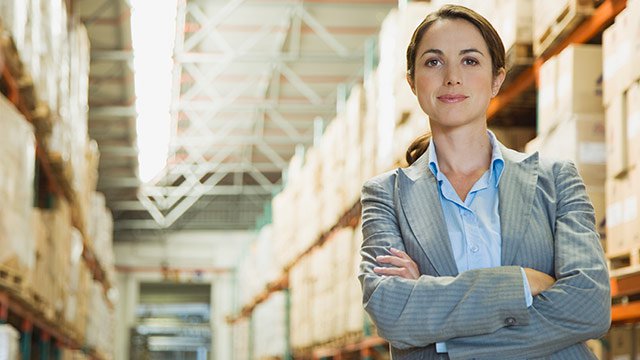
Advancing in a professional manager career in today’s competitive business environment usually takes initiative, self-motivation, and hard work. Most managers can no longer depend on an employer to provide a job long-term, promote from within or provide advanced training. Updating managerial skills to remain relevant to an organization is more than just good practice – it is one important part of a manager’s career success.
Candidates for industrial production manager jobs can gain necessary skills through Six Sigma training to help businesses improve productivity and reduce waste. In addition, enrolling in a Certificate in Six Sigma program can show employers that you are dedicated not only to your own professional education, but also to embracing organizational goals and improving profitability.
Industrial Production Manager Jobs: Potential Salary
According to U.S. Bureau of Labor Statistics (BLS), the average annual salary for industrial production managers was $103,380 as of 2018 data. With advanced training and certification, the professionals may have higher earning potential. BLS data showed that professional industrial production managers in the top 10% earned as much as $172,150 annually.
Compensation for industrial production manager jobs often varies by industry and employer, but the data showed that advanced training like Six Sigma Black Belt may increase earning potential. In most cases, the most demanded jobs are given to professionals with experience, specialized training, and industry-recognized certification.
Job Duties
Industrial production managers can help contribute to a firm’s bottom line by coordinating the people and processes involved in manufacturing. One of their most important duties can be ensuring production meets output and quality goals while remaining within budget limitations. Production managers may oversee one or more areas or an entire plant, depending on the employer and size of the operation.
To meet organizational production goals, industrial managers often develop new ways to use resources – whether human, material or capital – most efficiently. They may determine which machines to use and when, how many workers are needed to achieve maximum output and what the production sequence will be.
An industrial production manager job description usually includes developing budgets, approving expenditures for supplies and materials, and reviewing production orders for accuracy. They also typically develop production schedules and duty assignments, making strategic decisions as necessary to alter programs when time or budget limitations are reached.
Managers are typically responsible for supervising and mentoring a direct-report staff. Depending on the employer, the manager’s job duties may include hiring, training, evaluating and discharging workers, as well. Other duties related to staffing a manager may be responsible for include ensuring compliance with workplace safety programs and organizing and cross-training worker teams for maximum production flexibility.
Controlling costs is another important duty of an industrial production manager. They typically monitor every stage of production, analyze current methods and develop new ways to save steps, time and materials in order to reduce costs. Initiating and implementing programs to control inventory, improve efficiency and increase production may help enhance a manager’s value to the company.
When a product fails to meet quality standards, it is typically the production manager’s job to solve the problem. In modern manufacturing plants, advanced techniques such as Six Sigma are emphasized to ensure continuous quality improvement. Industrial production managers may be required to work with procurement staff, parts and materials vendors or individual workers to bring quality back up to standards.
Education and Training
Education and training requirements for industrial production manager jobs may vary by employer and industry. In most cases, employers prefer to hire managers with a bachelor’s degree and relevant experience.
Many production managers earn a bachelor’s degree in a related field – such as industrial technology, industrial engineering or business administration and pursue specialized training through executive education programs.
In addition, employers may prefer to hire candidates with Six Sigma certification. To gain the skills employers are looking for, some professionals can enroll in professional Six Sigma training – such as the 100% online certificate programs offered by Villanova University.
Professionals who complete Villanova’s Certificate in Six Sigma program can gain the knowledge and skills to:
- Implement proved Six Sigma problem-solving methods and statistical tools
- Improve production, reduce costs and successfully drive organizational change
- Master new processes for gathering and analyzing data
- Apply best practices for strengthening the bottom line
- Earn industry-recognized certifications
- Successfully compete for related jobs
Quality Skills
Industrial production managers can help contribute to the strength and competitiveness of a company with a broad range of skills. They regularly interface with everyone from management to support staff and production line workers, so strong written and verbal communication skills are often crucial. Guiding a diverse team toward a common goal can take strong leadership skills, and keeping a production facility profitable usually takes focus, problem-solving and analytical skills.
Employers may also prefer candidates with advanced training and certification. Villanova’s online Six Sigma training programs can equip professionals with the knowledge and skills to help stand out from the crowd.