Failure Mode Effect Analysis (FMEA)
Last Updated May 8, 2019
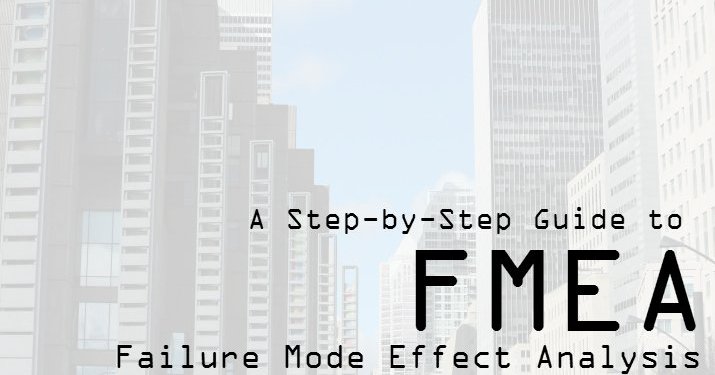
Six Sigma has a low tolerance for failure. The name Six Sigma itself allows no more than 3.4 defects per million opportunities. This rigorous methodology focuses on eliminating the fluctuations in production that cause defects and failure.
Failure Mode Effect Analysis (FMEA) is a valuable tool in this quest to reduce and eliminate defects. FMEA uses systematic methods to evaluate a process for identifying where and how it might fail, and to gauge the potential impact of different types of failures. FMEA then acts to identify the parts of the process that are most in need of change. FMEA provides an in-depth investigation of the following:
- Steps in the process
- What could go wrong
- Why might the failure happen
- What would be the consequences of each failure
When to Use FMEA
The FMEA methodology can improve products, processes and services. The most common reason for performing an FMEA study is to help the Six Sigma project team act to prevent a failure. FMEA can be used in the following situations:
- Designing or redesigning a product or service
- Attempting to apply an existing process, product or service in a new way.
- Developing control plans for a new or redesigned process
- Planning improvement goals for an existing process, product or service
- Analyzing failures of an existing process, product or service
- Maintaining the quality of a process, product or service
12 Easy Steps to FMEA
This versatile tool can be implemented in a series of steps. The process required to perform an FMEA study has elements in common with the steps in completing the DMAIC cycle:
- Bring together a team of cross-functional experts with knowledge about the process, product or service and the customer’s needs.
- Create the scope of the FMEA study. Decide whether it will be applied to concept, system, design, process or service. Clearly define the scope to ensure that every team member understands it in detail.
- Start by asking “What is the purpose of the process? What do customers expect it to do?” This will help break the process or service into its individual parts and process steps.
- Identify all the ways failure could happen (failure mode) for each step of the process.
- For each failure mode, identify all the consequences on the process. Ask, “How does failure impact the customer? What are the consequences of failure?”
- Assign a severity rating for each failure on a scale from 1 to 10, 1 is unimportant and 10 is a disaster.
- Determine the root causes for each failure mode.
- Assign each mode an occurrence rating from 1 to 10, 1 is extremely unlikely and 10 is a virtual certainty.
- List current process controls for the cause of each failure: tests, mechanisms or controls that prevent failures from impacting the customer.
- Give each process control a detection rating of how well the control can detect failure. Again, this is on a scale from 1 to 10; a rating of 1 is the certainty that the control can detect a failure, and 10 means there is no control in place.
- Calculate the risk priority number, or RPN, which equals severity × occurrence × detection ratings. Determine criticality by multiplying severity by the occurrence. These figures help identify areas of potential failure and allow the team to rank them.
- Recommend actions that reduce the severity or occurrence of failure. Assign responsibility and completion dates for these actions and target dates for their completion.