The Benefits and Challenges of Lean Manufacturing
Last Updated October 24, 2019
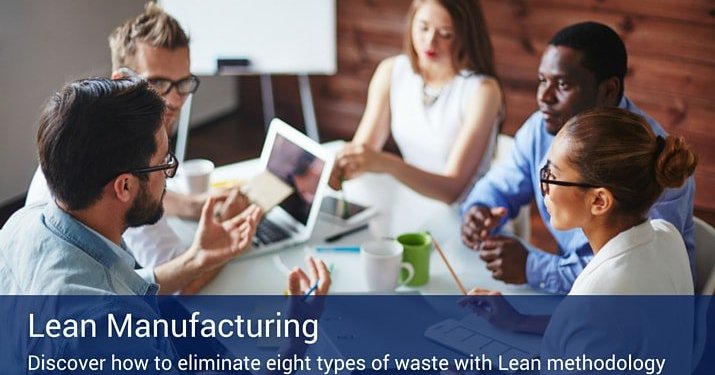
Companies are attracted to Lean manufacturing because Lean helps organizations do more with less. Lean’s two guiding principles are first, satisfy the customer’s needs, and second, do it at a profit.
Lean evaluates every aspect of the process with these two imperatives in mind. Everything that does not meet this dual objective is considered waste and is eliminated. Lean methodology teaches that there are eight different types of waste, and then focuses on eliminating them. These eight wastes include:
- Transport – Moving materials and product needlessly
- Inventory – Keeping more products than needed on-site
- Motion – Workers make unneeded movements in the production process
- Waiting – A product that sits idle while no value is added
- Over Processing – Doing more work than the customer requires
- Over Production – Creating more product than the customer currently demands
- Defects – Production errors that impact the customer
- Undeveloped Talent – Falling short of using employees talents, abilities and skills
Eliminating waste delivers several benefits to the company and its employees. Here are the most common ways in which Lean can help:
- Higher efficiency – Once your team has eliminated unneeded product transportation, employee movement that adds no value, and products sitting idle, efficiency increases. Reducing the defects that require expensive inspection and rework also help to boost efficiency.
- Better quality – Lean’s focus on getting rid of defects puts quality at the center of attention. Lean assists project teams to identify the root causes of defects and then helps improve the production process to eliminate them. Improving processes is a long-term solution for reducing defects and improving quality.
- Better use of employees – Lean cuts overproduction by adjusting production to meet customer demand, and it simplifies the product to eliminate extra processing. These activities help your company meet customer demand with fewer employees. Fortunately, this doesn’t require layoffs. Lean mandates that these employees be trained and reassigned to better use their talents.
- Optimize space – Lean principles help reduce excess inventory and eliminate overproducing products. When you are producing no more than what the customer requires and you are shipping all of your products quickly, there will be more physical space on the production floor. This environment is easier to organize and safer to work in.
- Happier employees – As employees are given a chance to increase their skills and abilities, and to fully develop their talent, they will be more supportive of Lean.
While practicing Lean pays big dividends, it also generates some challenges. Always be aware of the following possible hurdles:
- Expense – It costs money to acquire the right equipment or update the production line, and these costs have to be covered before your company can begin seeing the benefits of Lean. It takes time to reap the payoff.
- More outlays for labor – Making the changes dictated by Lean also requires an up-front commitment to temporary labor. This increases labor costs briefly while improvements are being put into place, but ultimately, labor cost reductions will follow.
- Opposition – People fear innovations – even the ones that bring improvement. Setting aside old practices and processes can be difficult for some employees. Assure them with proper training and education.
Lean principles can provide substantial gains for organizations and their employees. As long as they understand its benefits and challenges, implementing a Lean improvement strategy can make a positive difference in company morale, customer satisfaction and the organization’s bottom line.