How to Avoid the Strategic Pitfalls of Implementing Six Sigma
Last Updated May 3, 2019
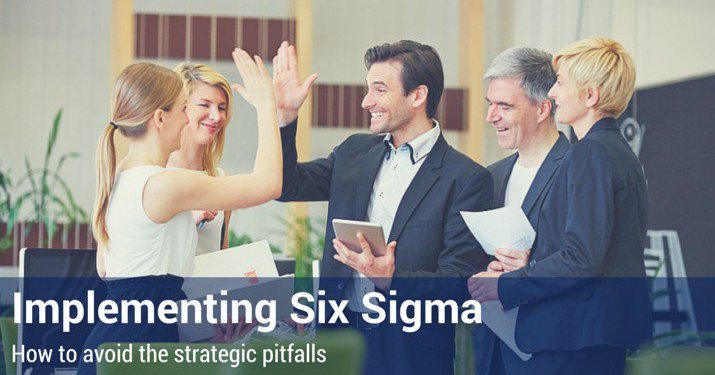
Professionals interested in implementing Six Sigma principles in their company or earning a Six Sigma certification are likely familiar with the rich benefits it can generate, including:
- Increasing Revenue – Six Sigma makes a process more efficient by reducing defects. Processes that have been streamlined by the Six Sigma methodology can produce more output with less rework at the same cost. This increased productivity leads to higher revenue.
- Decreasing Costs – The defects in an inefficient process cause waste in time and materials that increase production costs. Six Sigma helps reduce the number of defects and aims to decrease waste. This helps lower production costs.
- Improving Efficiency – Six Sigma increases process capacity by reducing defects and material waste and enables organizations to do more with the same amount of resources.
Six Sigma principles can transform an organization’s operations and enhance its financial performance. However, like any improvement methodology, Six Sigma may produce poor results when it is applied improperly.
While Six Sigma has been proven to work, it is sometimes deployed as part of a flawed strategy. Practitioners would do well to watch for the following strategic blunders, and apply the recommended solutions, to recognize the full promise of Six Sigma.
Potential Pitfalls for Six Sigma Projects
- Disconnect from Business Goals – If the project scope or the organization’s goals are unclear, a Six Sigma project team may end up working on a project with no direct link to the organization’s objectives. A Six Sigma project that does not advance its company’s goals is doomed to irrelevance even if it meets its own objectives.
Solution: Leadership can rank projects according to its business goals. This ensures that Six Sigma projects help advance the organization’s objectives. Ranking projects by the greatest business impact can help companies determine which ones should be deployed first.
- Playing Politics – In its purest form, Six Sigma is a process improvement methodology and no more. Some authorities, however, misuse Six Sigma by using it to promote a hidden agenda.
Solution: Keep the project selection process honest by aligning it with corporate goals that bring long-term benefit to the entire business instead of serving the narrow interests of select departments.
- Picking the Wrong Projects – In a hurry to reap the benefits of Six Sigma process improvement, leadership can sometimes mandate projects that are outside the team’s realm of control and expertise, or do not focus on business objectives.
Solution: Requiring Six Sigma projects to meet certain standards before they are deployed helps prevent businesses from wasting resources on quality improvement efforts that are likely to fail. Requirements for Six Sigma projects can include a meaningful impact on business objectives, a measurable financial benefit, a clear process improvement and an enhanced customer satisfaction.
- Lack of Leadership Support – Project teams rely on leadership for financial support and help overcoming obstacles to change. Without active support from upper management, Six Sigma projects can go underfunded and any changes they make tend to be short-lived.
Solution: Project teams can overcome neglect from leadership by promoting the potential value of the project. When money talks, management listens. Also, include top leadership in projects when possible to keep them fully engaged.
- Teams Lack Balance – All functions touched by the process should be represented on the project team. However, because time and resources are limited and departments tend to be siloed, this doesn’t always happen. This results in incomplete solutions and meager improvement.
Solution: Project teams can be expanded to include between 6 to 10 people encompassing all relevant departments without diminishing performance. If employees are not able to participate as full-time team members, they can be added as supporting contributors.
- Excluding Functional Experts – Employees best acquainted with how a process works, or fails to work, are the frontline employees who use it every day. These functional experts have a wealth of practical process knowledge that is critical in identifying problems, creating solutions and implementing improvements. Six Sigma teams benefit from hands-on experience with the process and the knowledge of functional experts. Without these critical elements, teams risk developing only a theoretical understanding of the process and missing out on practical solutions.
Solution: Project teams understand the process better when they include frontline workers with functional expertise. Also, team members who take the time to walk through the process can gain a clear understanding of how it works and have a greater chance of creating practical solutions.
- Expecting Results Too Soon – Six Sigma projects begin with high expectations, including the anticipation that the project will be concluded in a realistically unreasonable amount of time. Six Sigma is partly an art that cannot be rushed and must be allowed to develop organically. Another factor that adds time to the completion of a Six Sigma project is that teams typically include Green Belts, who dedicate a part-time effort to Six Sigma while working their regular jobs.
Solution: Six Sigma Champions and Master Black Belts can help manage the company’s expectations about project completion time. And when project teams provide regular progress reports, they keep stakeholders from expecting too much progress too soon.
Like any methodology, Six Sigma produces poor results when it is applied improperly. Six Sigma projects perform poorly when a strategy works against them. They face possible pitfalls in leadership, the team dynamic, and stakeholder expectations. Awareness is the key to improvement. Recognizing potential problems and implementing solutions quickly can help ensure Six Sigma project success.