Saving Money with Lean Pt 2
Last Updated January 17, 2020
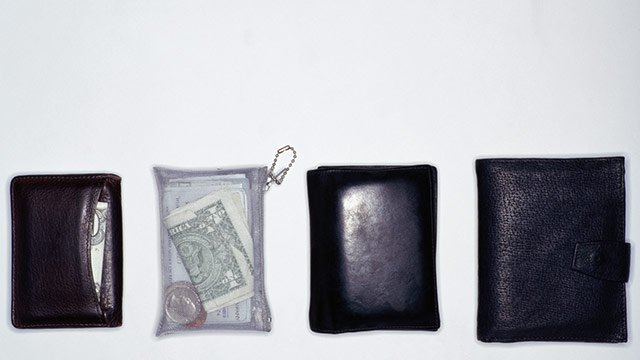
When a project is based on an implementation plan that has well-defined objectives, deliverables, milestones, and schedules, it has a greater chance of generating cost savings.
Steering committees should meet regularly to review actions, reassign responsibilities as needed, and hold teams accountable for results.
Status reports should be reviewed with financial partners, project teams, suppliers, and customers to ensure supply and delivery streams are supporting the project’s objectives without generating additional costs.
Promote Results and Showcase People
Don’t keep success a secret. Positive results from Lean Six Sigma projects should be recognized throughout an organization. Keeping cost savings, exemplary staff performance or waste reduction quiet does not encourage more of the same.
A better idea is to post the Lean strategy and individuals who have pursued Six Sigma training, along with current projects and achievements, on a company-wide dashboard, where everyone in the organization can see it. Not only does this create a sense of common purpose – it can result in healthy competition.
Another big benefit of publicizing results and individual achievement is that it fosters greater buy-in of Six Sigma training and principles.
Change is an integral, continuous part of successful organizations. Those unwilling or unable to embrace it may become part of the problem.
Identifying Waste Means it Can Be Reduced
Lean manufacturing is based on principles developed by Toyota, where identifying and reducing waste is essential to running a profitable organization.
The types of waste identified in Lean manufacturing are:
- Muri: The waste due to overburden. Muri means workers have too much to do or ineffective tools with which to do their jobs. Poorly organized workspaces are one example, which can be addressed with the 5S method
- 5S: 5S means sorting, straightening, sweeping or shining, standardizing, and sustaining. With Muri eliminated, efficiency and quality can be improved
- Mura: The waste due to inconsistency or fluctuations, either in inventory levels or quality issues. Mura is reduced through Just-in-Time inventory systems, where little or no inventory is carried and the organization always has the right amount of inventory at the right time
- Muda: The wasteful and unproductive activities within an organization. Muda activities do not add value; Muda is the antithesis of Lean. Lean processes add value to goods or services that customers will pay for
Lean and Six Sigma for a Stronger Bottom Line
Strengthening revenue by utilizing Lean manufacturing and Six Sigma tools can greatly impact an organization’s bottom line. For some projects, immediate cost savings can be realized. In others, small savings add up over time.
Finding ways to demonstrate Lean Six Sigma’s positive impact is important to keeping the entire organization moving forward for continuous improvement.
Remember, if the numbers aren’t where they should be, reevaluate. Go back to the beginning, reconfigure the approach and gain a new perspective.
Starting over can ultimately save time and energy while helping to achieve the results the company expects.